Material
carbone steel (O1,O2, XC...., file)
2 chigago screw (5mm of diameter and M4)
4 screw M4
2 thin wascher
Tool
Grinder (or file

belt sander (40,120,80,220)
1 dremel with cutting disk and sand drum
Screw driver
1 drill press with drill bit of 5 mm and 4 mm
Some thing to keep the piece in place
1 grip
1 hamer
1 point
1 torch
1 l of oil
1 kitchen oven
Glove, glas, mask....
Take a piece of steek and draw the blade form. The heel is in bevel because that is the part where hit the nail. (i take some margin to adjust after)
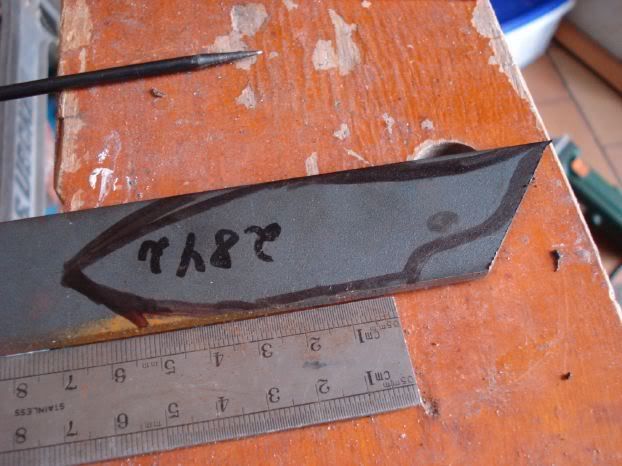
Cut the steel with the grinder and put the blade in form. (don't forget to cool frequently the steel).
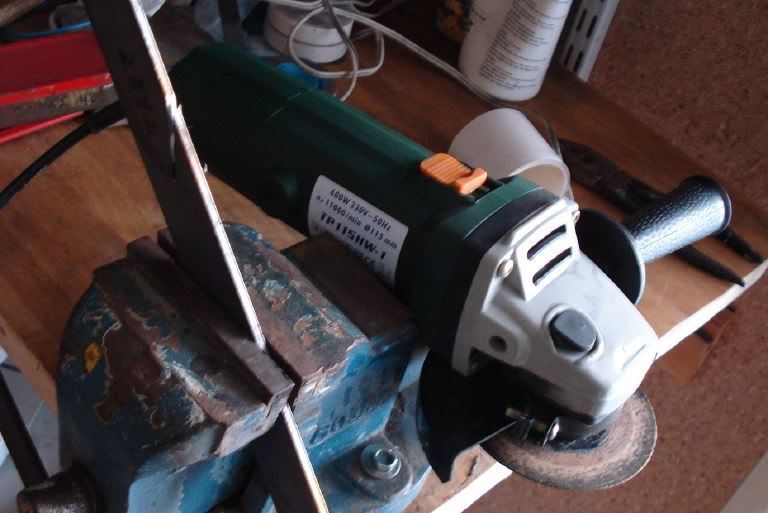
After the work.
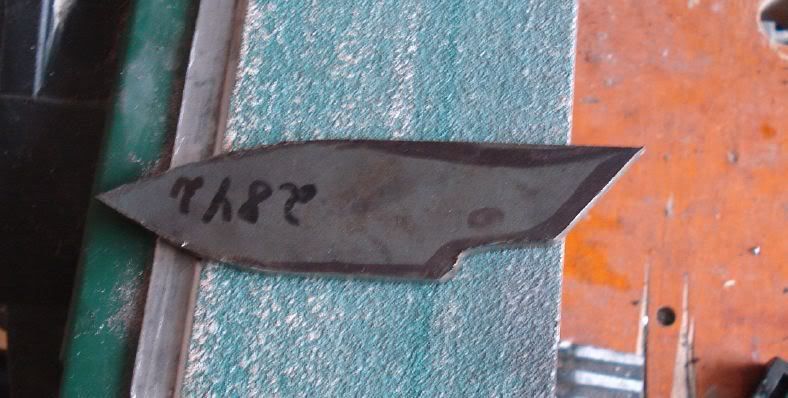
Drill the hole of 5 mm for the pivot. Marked the point with the point and the hammer.
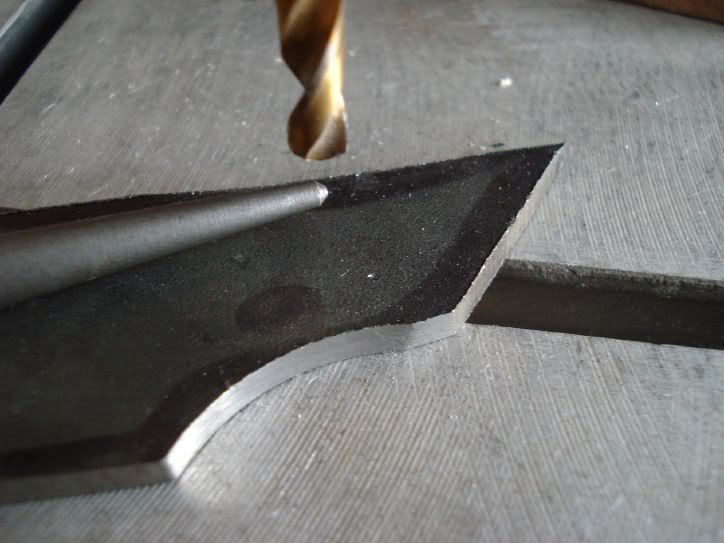
One hole
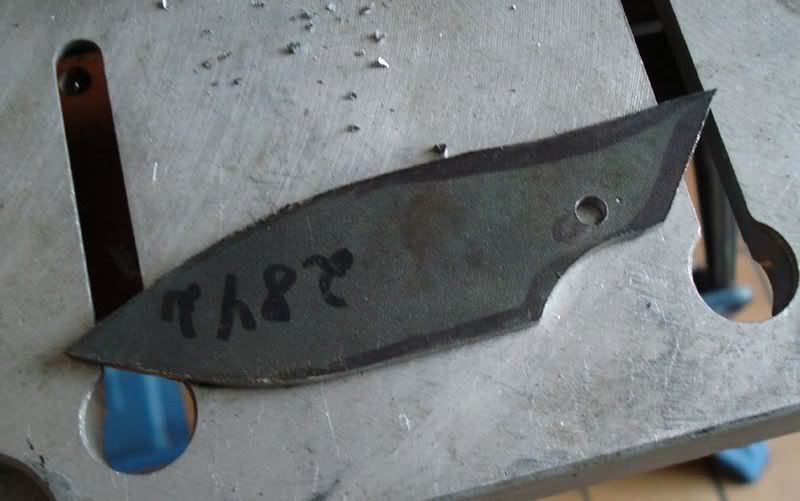
Fix in vice the blade blade to the top. And center the futur edge with the grinder.
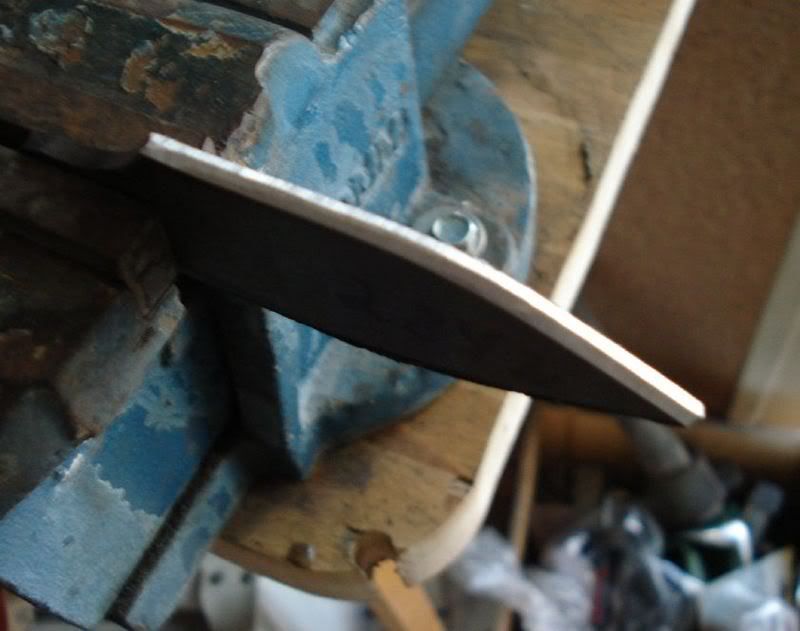
You can make the bevel, i draw the top of the bevel with a pen, and after i work with the grinder, heel to point, en edge to back of the blade. Slowly without pressure

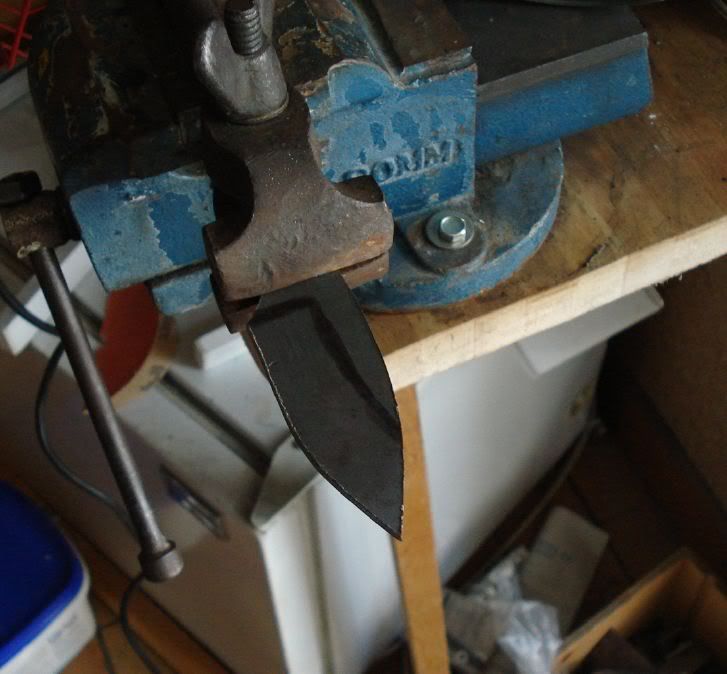
Same thing on the other face, avoid to be too thin to the edge level.
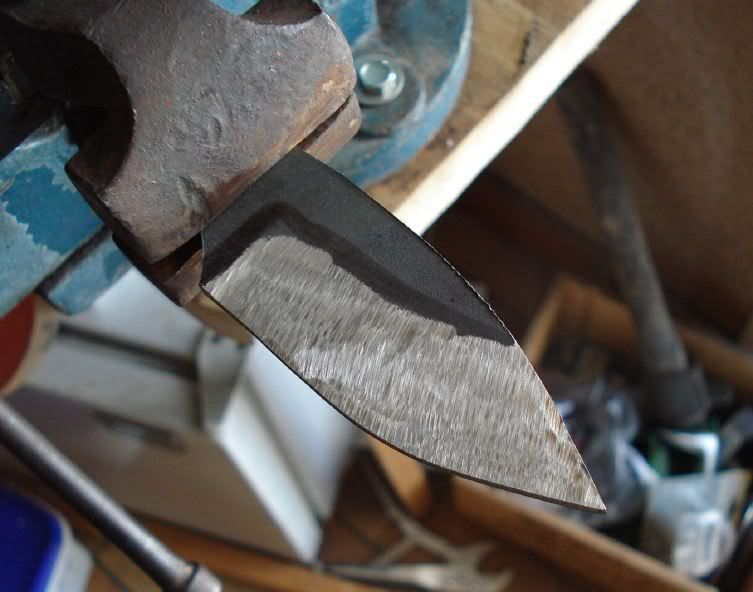
Continu the bevel with the belt sander, grit 40, 80. cool the blade frequently. Keep 1 mm to the edge for the heat treat.
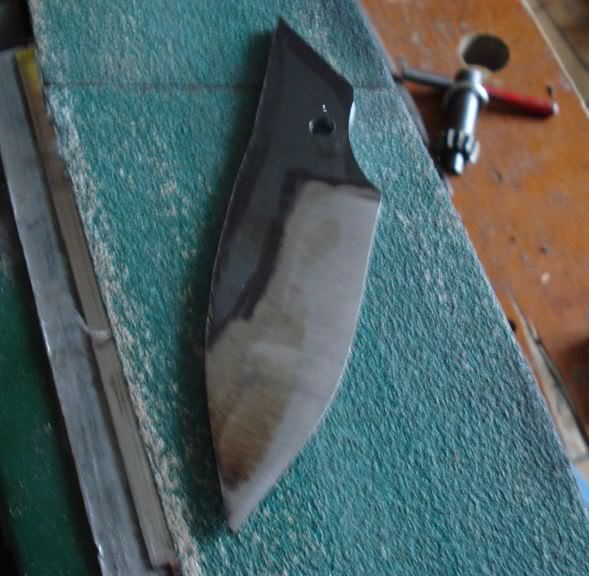
Give a little passage of 120 grit on the edge in order to make disapear all the scratch and mark.
Make 3 normalisation, heat the steel to the red cherry and keep it cool slowly three time . (red cherry, when the magnet don't attrack the steel).
take the oil and heat it around 60-70°
With a grip take the blade and heat it with the torch, wait the magnet stop to attrack the steel, continu to heat around 40s 1 m, in order to be totaly in the temperature of transformation and put the blade in the oil.
After the quench,if the file on the edge slid, it's perfect. If it's bite the material. Retry to normalised and to harden.
Make the tempering in the kitchen furnace, 1 hour to 220°C and let cool to the room température.
You can finish the bevel with the belt sander grit 80,120,220. And you can polish the blade with felter and polish paste.
I drilled the blade just for the design, if you want to make it so, make it before the heat treatment

handle
Take a plate of steel (here ti plate of 1,8mm) but every steel plate inferior to 3mm will be great.
Mark the pivot point with the hammer and the point. Drill to 5 mm with the drill press.
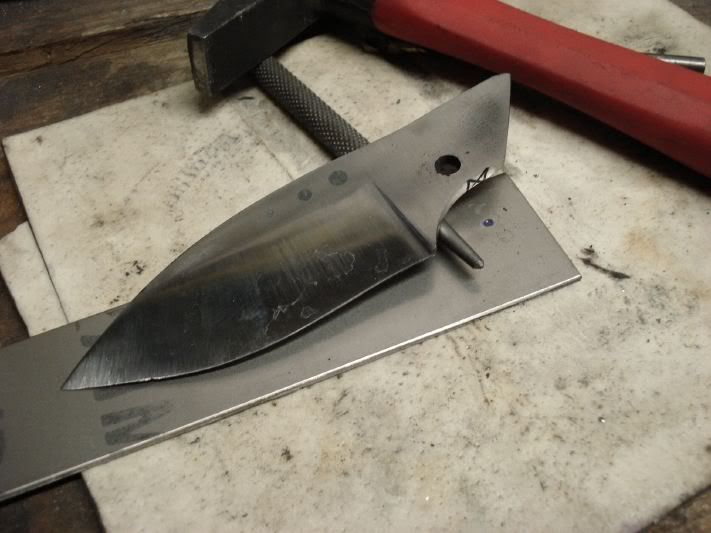
Put the pivot in the hole, and the blade on it, pivot the blade and mark the point where to drill the second hole for the nail. Drill with the 4mm drill bit.
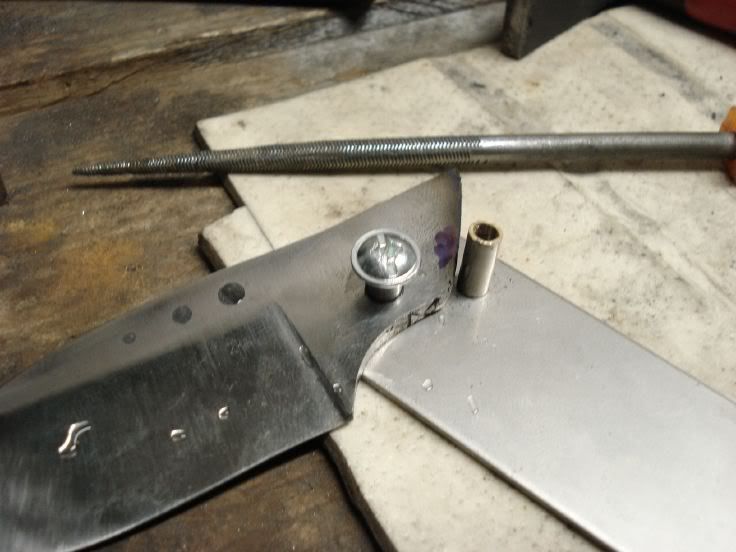
The second nail is in place, pivot the blade. You have to mod the heel of the blade to adjust it. (i conserved a lot of material, recut it and adjust it with dremel little sand drum).
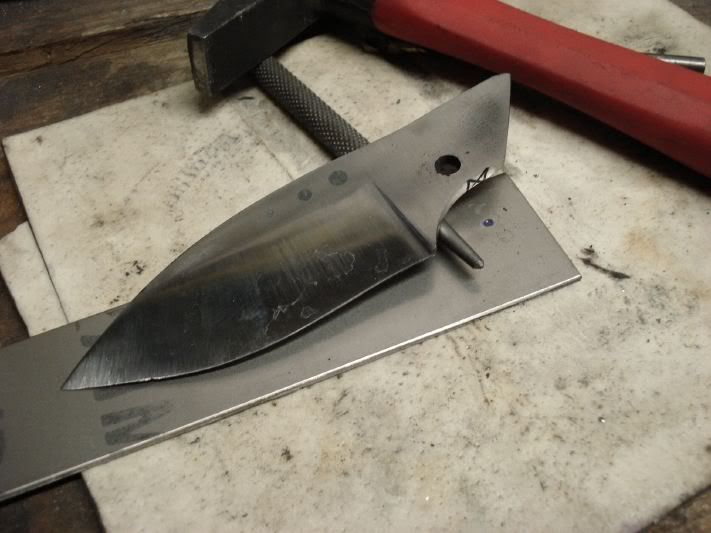
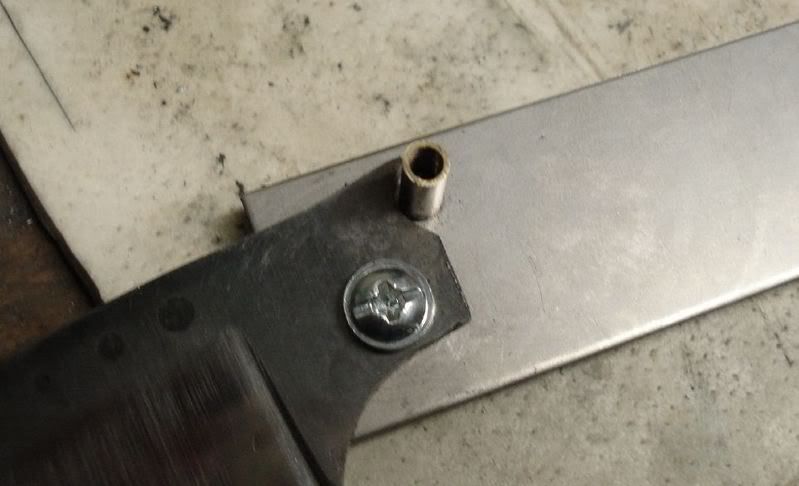
Good open and closed.
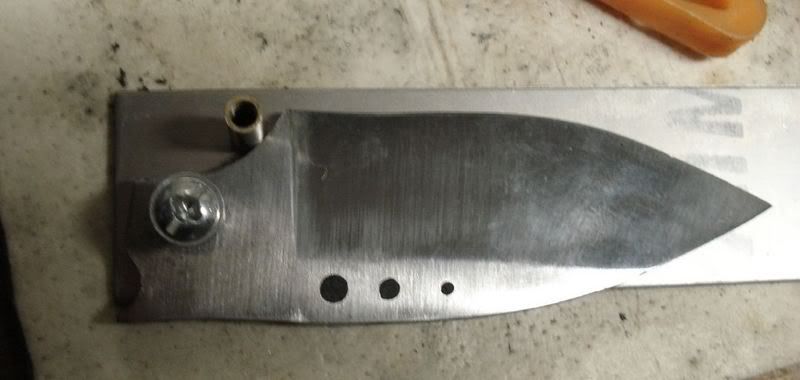
Now we fold the handle, mark the line of folding to 5 mm of the tip of the point.
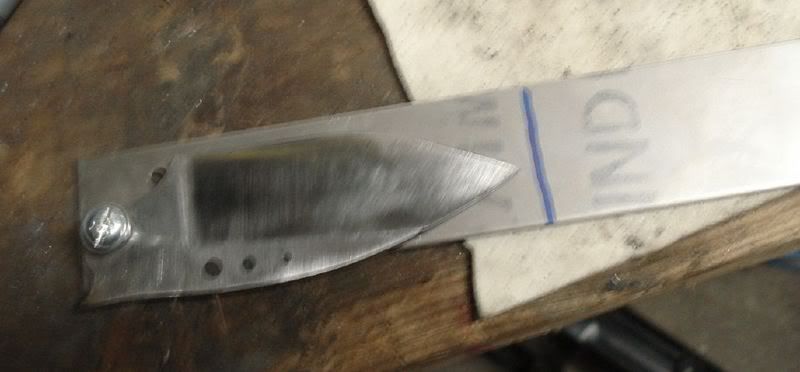
fix the plate with a steel piece of the thickness of the blade on it. the end of the steel plate is to 5 mm of the line of foldin.
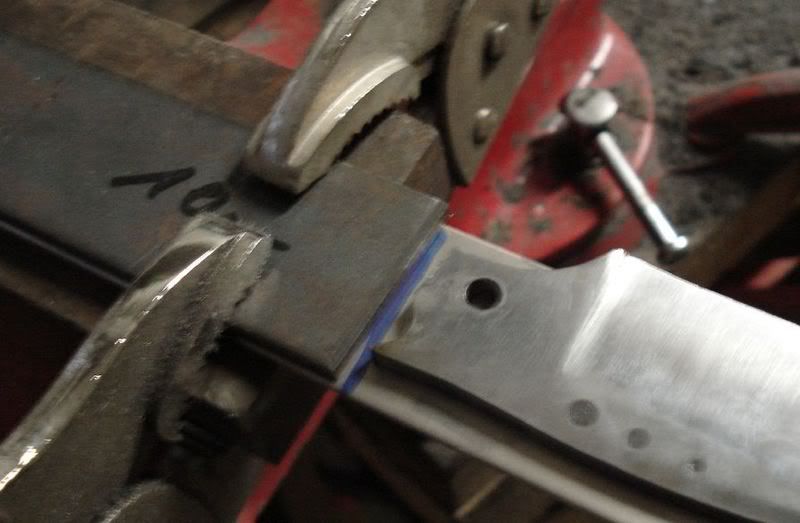
Heat with the torch to the flex point, and hammer the part that you heat in order to fold the material. Stop to heat, cool everything in water (use grip to manipulate the piece

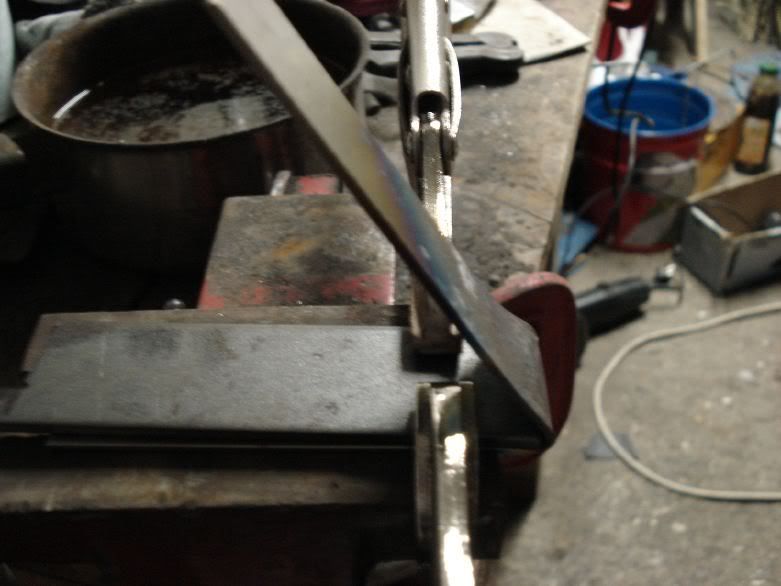
The point move perfectly. you can continu.
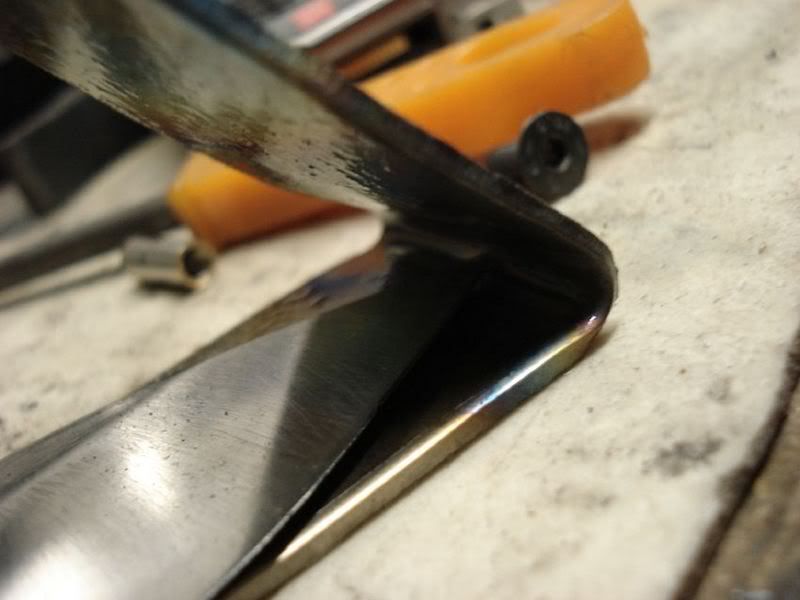
Fix everything with the grip vice far away of the part you want to fold. Reheat and continu to hammer to fold the plate.
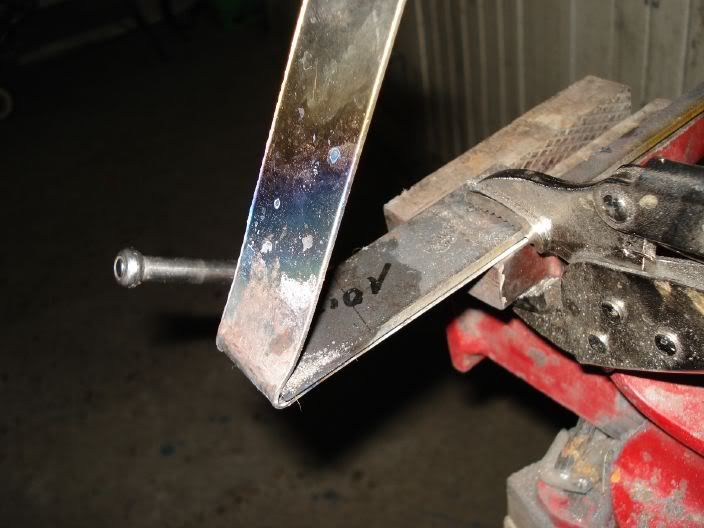
Dismantle, cool the piece (it's always hot use grip), take the piece in a vice hell to the floor with the steel plate in the plate to fold. Heat the point of flexion and tigh the vice.

It's possible that the fold the material is not centered, put the plate in the vice heat the heal and recenter everything with the hammer.
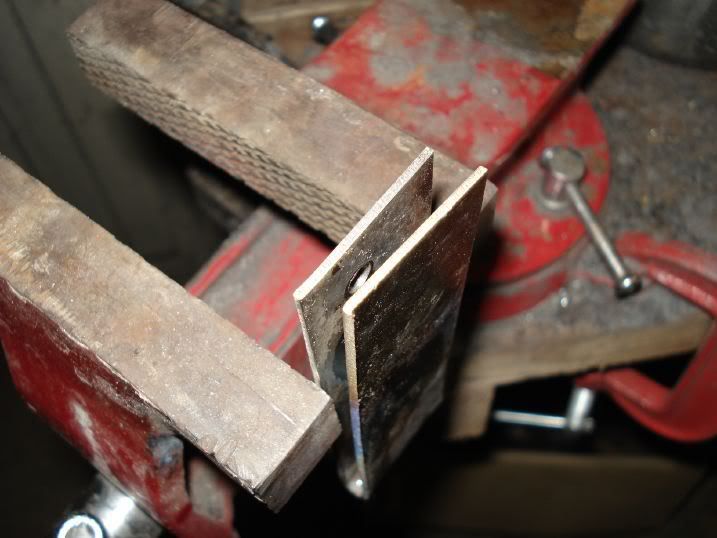
To adjust the handle, put the handle with the steel piece in it in a vice, heat the heel, and tigh the vice. Cool everything, and it's good.
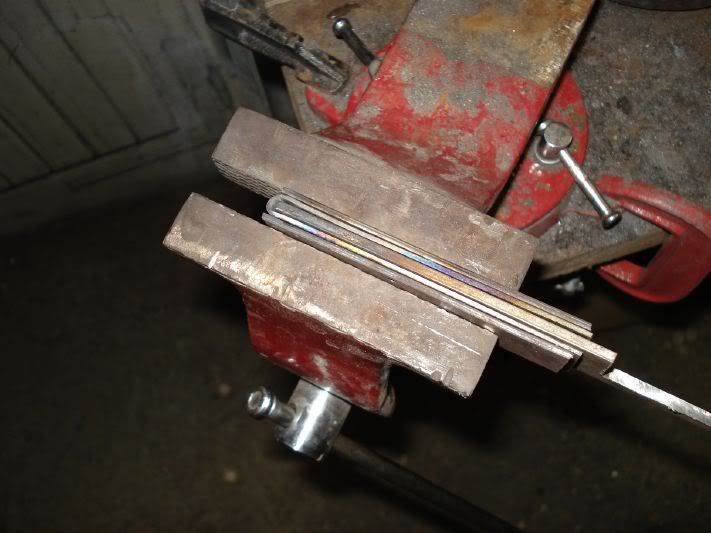
Drill the hole in the hole existend.
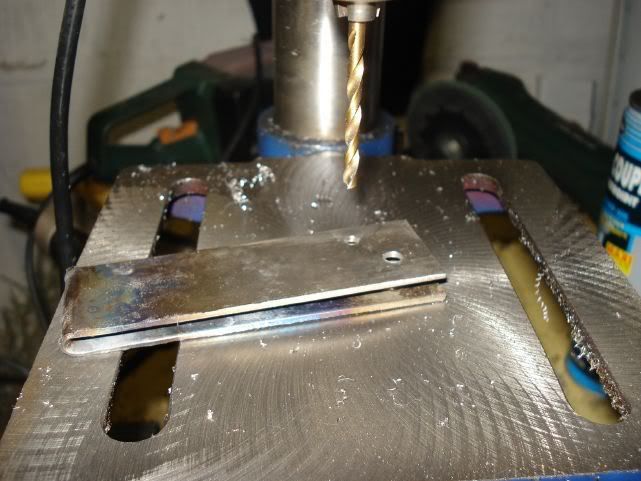
Draw the handle form on the handle.
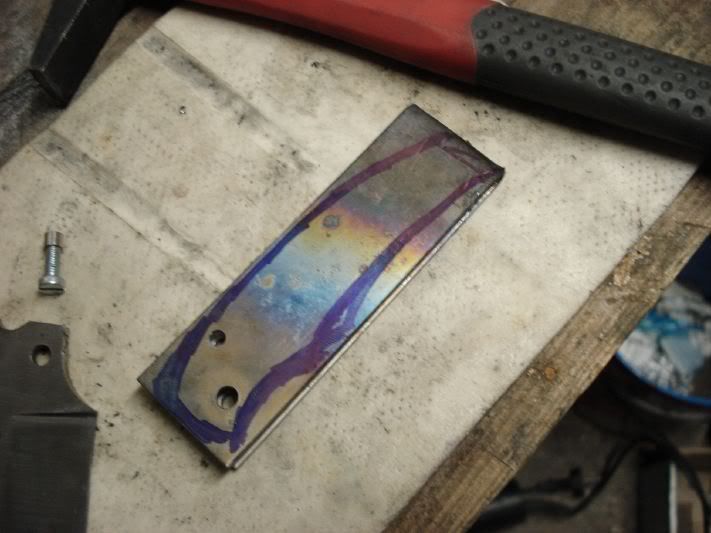
Fixed the piece in vice, and make the handle in form with the grinder and after with the belt sander.You can finish with the dremel and sand drum if you want. The photo is hust after the grind work.
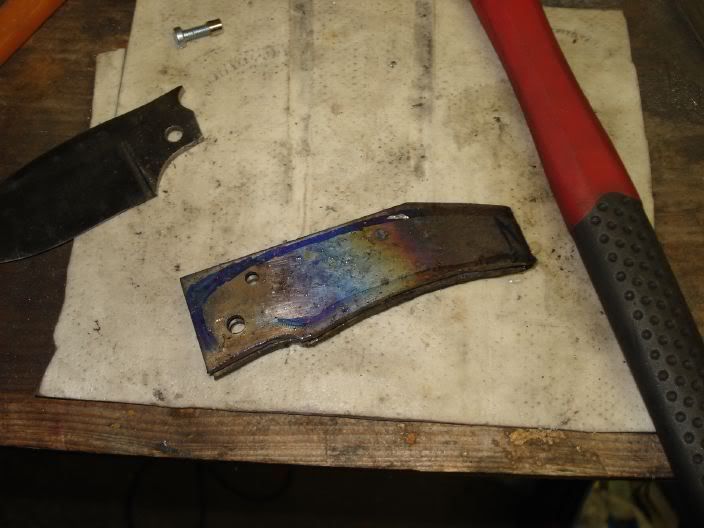
When the form is finish, sand the handle with the belt sand in order to make disapear the mark or heat


Little piece
Pivot
Cut the chicago screw with the cutting disk of dremel.
The size is
Blade thickness+Handle thickness (only the thickness of the plate)+ washer thickness.
(ici 3,2+1,8+0,2. soit 5,2 mm.
Everything must to be clean and plan.
For the nail
same thing,
Blade thickness + Washer Thickness (3,4mm here)

Screw
I haven't got BTR or torx button or round heat under the hand, i took simple philips screx that i mod a little.
Put the screw in the drill machine, make it turn slowly and work with a file in order to round it. After use some sand paper to clean the screw.
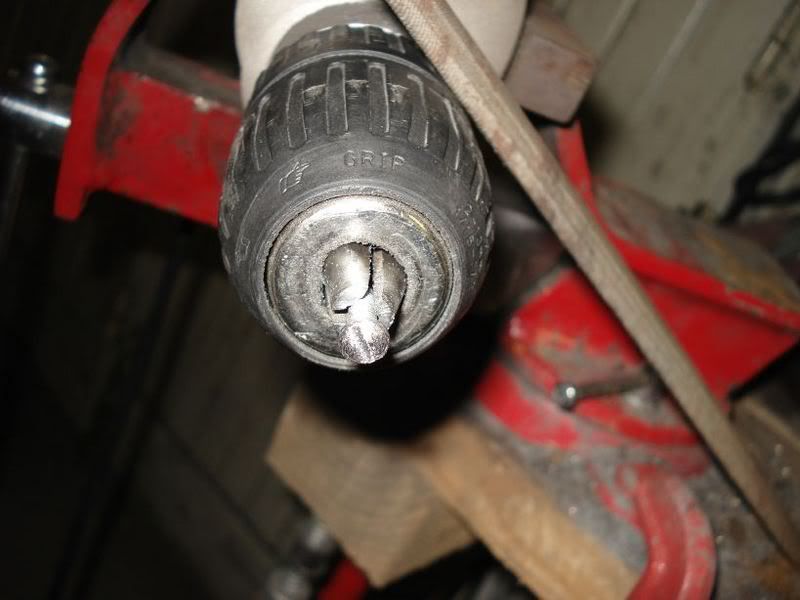
With cutting disk you can make a file work (3 mark on each side

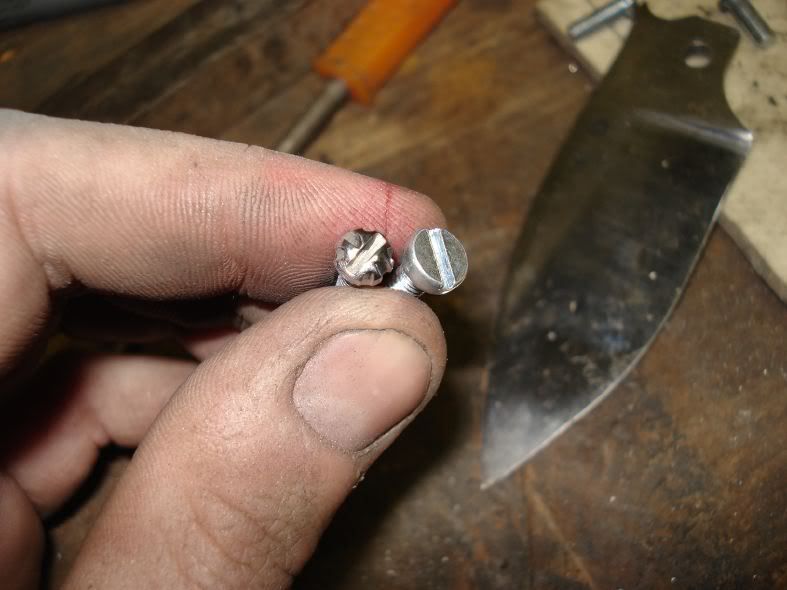
Cut the screw to 3 mm,
Assembly
nous avons
1 blade
1 handle
4 screw
1 "nail"
1 pivot
the washer aren't here because i injured me with some washer yesterday and don't have the pleasure to remake another. I will make some for the next week and put it on the knife after

One time the assembly is made, you have to sharpen it. And you have your knife.
8 hour of work (2 for the blade and 6 for the handle and screw).
I hope you enjoy
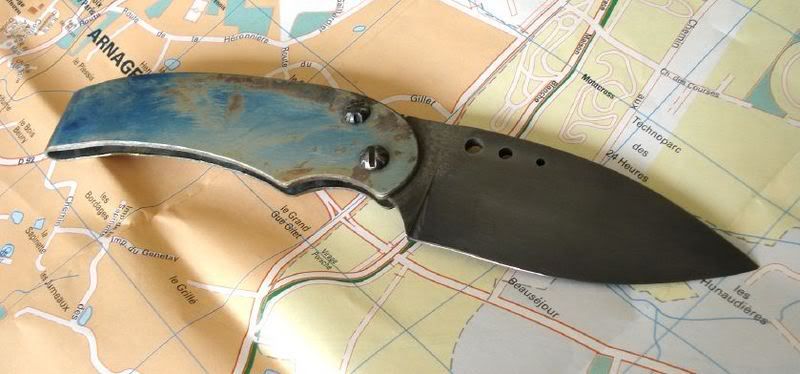
More picture here
http://www.talkblade.info/viewtopic.php?p=130116#130116